PRACTICALLY SPEAKING - How to determine where to target machine improvements
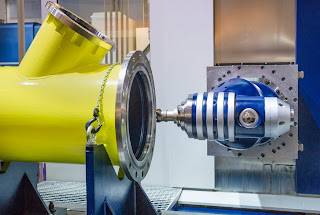
Follow a simple
3-step process.
Step 1: Focus. Trying
to fix everything all at once will ensure that there will lots of effort
expended with little return in either the short- or medium-term. Start by
focusing on known bottlenecks. These are usually best identified via regular
walks through the value stream (known as a GEMBA walk) and by simply asking
employees about trouble spots. A few machines almost always have piles of work
in front of them while the work at other machines ebbs and flows.
Step 2: Gather data. This
can be done manually in the short-term quite easily. It may involve little more
than dutifully recording key information on a chart kept close to the equipment
and entering the data into a spreadsheet for analysis. There are even sample
data collection forms available online that could be tailored to your specific
needs. For firms planning on implementing an IIoT (Industrial Internet of
Things) strategy, just a few machines can serve as a proof-of-concept or pilot
project before investing heavily in a technology solution. Some solution
providers, such as Forcam GmbH (www.forcam.com) and 42Q (www.42-q.com),
have start-up packages to get automated data collection installed and working quickly
on a handful of machines.
Whether collecting data manually, or through a software application,
operators will have to input some of the reasons for, and frequencies of,
events that occur. To facilitate this, predefine some standardized reason codes for items related
unplanned downtime, low performance and impacts on quality.
These can be modified along the way based on the frequency of occurrence.
Step 3: Analysis.
Analyse the data to determine a course of action. Standard techniques, such as
histograms and Pareto analysis, will go a long way to being able to see the top
few reasons for not achieving goals in one aspect or another.
Don’t jump to
conclusions
I had an experience where there was a big emphasis from
executive management to focus on operator performance to standard time. Fortunately,
I was able to hold off and wait for the results of an initial period of data
collection. The analysis showed that although standard times could be improved,
the BIGGEST improvements were to be found simply in keeping the machine running
(productively). Without the data, we would have been going down the wrong path.
By the numbers
Bring this all together by using OEE (Overall Equipment
Effectiveness) in a judicious manner. OEE is comprised of three separate
components:
Availability – a comparison of the scheduled operating time
that the equipment is actually operating
Performance – a comparison of the speed at which the
equipment is operating versus the speed at which it is designed to operate
Quality – the ratio of good parts produced to total parts
produced
A worked example of the calculation is shown in the attached
image. The boxes highlighted in blue represent the data that users must collect
and enter. The rest is calculated by formula. Beyond these figures, operators
must be recording reasons and frequencies relating to key events (see step 2
above).
OEE can be used as a high-level indicator and, to some extent, as a comparison between pieces of equipment or even between companies in order to identify a starting point. Its real power is in determining direction by allowing you to answer the question – are we getting better? Exercise caution, maximizing OEE is not the end goal. Improperly used, chasing OEE can lead to poor behaviours, such as running large batches to reduce changeovers and trying to hit peak performance inside those batches.
OEE can be used as a high-level indicator and, to some extent, as a comparison between pieces of equipment or even between companies in order to identify a starting point. Its real power is in determining direction by allowing you to answer the question – are we getting better? Exercise caution, maximizing OEE is not the end goal. Improperly used, chasing OEE can lead to poor behaviours, such as running large batches to reduce changeovers and trying to hit peak performance inside those batches.
People use Availability, Performance, and Quality as second
level indicators of where to focus improvement efforts or to determine where to
collect more, or more detailed, data for further analysis. These metrics can
guide us toward the right approach, whether it be to implement SMED (Single
Minute Exchange of Die), 5S, or Kaizen to name a few of the key lean approaches
available.
Companies should also look at TEEP (Total Effective
Equipment Performance) because it introduces the concept of Loading to the
equation. Loading is the percentage of calendar time that equipment is
scheduled to run. From total of 7 days of 24 hours in a week, we need to subtract
planned non-working days, non-working shifts within a workday, and scheduled
maintenance. This comes together with OEE as per the formula:
TEEP = Loading x OEE
Significant improvement in TEEP and OEE can come quickly by
working with employees and supervision to add shifts, stagger breaks, implement
TPM (Total Preventive Maintenance), and other approaches.
TAKEAWAYS: Use
data to drive decision-making. Look first for the low-hanging fruit. Don’t
chase the metric to the exclusion of good practice.
NOTE: A version of this article was published in Valve World Magazine 2018-09
Comments
Post a Comment